会員向け情報
研究室紹介
土浦素形材工場の紹介
2007年4月1日に自動車鋳物㈱、㈱ジックマテリアル、いすゞキャステック㈱といういすゞグループの鋳物会社3社が統合して我が社はスタートしました。資本金は14億8,000万円、総従業員数は約1,100人、鋳物素材の生産能力は月産で約15,000t。
ここでは関東支部でお馴染みの土浦素形材工場を紹介します。
操業開始は昭和45年4月。ダクタイル鋳鉄の生産が開始された当初の球状化処理方法はキャンデー法。置き注ぎ法はその後安定したマグネシウム合金が流布するようになり、処理取鍋や添加法などの工夫を重ねて現在の工法の姿になったと先輩達から伝えられてきております。昭和56年に稼動開始した当時生型では最大級のAMS造型機。その後、中物小物の量産品が北茨城工場に移管され、旧ラインを撤去して平成10年に導入したKDM造型機。2つの造型ラインで構成されています。表1に概要を示します。また図1にKDM造型機の特徴を示します。
項目 | KDM-6TSライン | AMS-14型ライン |
生産能力(t/月) | 1,400 | 1,200 |
枠サイズ(mm) | 600×700×300/250 | 1,500×1,100×400/400 |
サイクルタイム(秒/枠) | 20 | 160 |
注湯機 | 自動注湯装置2台 | 自動注湯装置1台 |
混練機 | シンプソン型(3トン/回×2基) | アイリッヒミル(2.3トン/回×1基) |
砂搬送 | パイプコンベア2本 | ベルトコンベア |
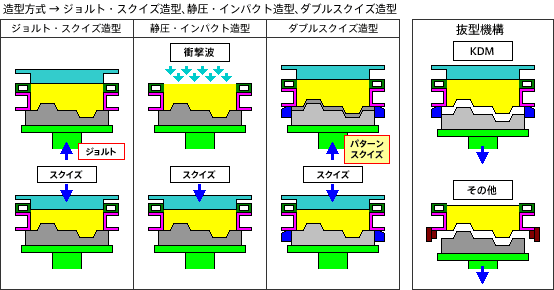
図1 KDM造型機の特徴
(パターンスクイズを加えたダブルスクイズと抜型機構の工夫により模型取り付けRを3から0.5が可能となり中子レス、バリレスへ。)
製品としてはエキゾーストマニホールドのような薄肉品やトラックや建設機械、油圧部品用の多種な小物のダクタイル鋳鉄素材部品と油圧バルブやアクスルハウジングのような大物の油圧機械や建設機械用部品のダクタイル鋳鉄鋳物素材を製造しています。
鋳物素材の製造方法で特徴的なのは、工場設立時に考案されたオートカットランナーによる鋳造方案の採用です。図2にその原理を示します。鋳物工場で最も過酷な作業の
一つである湯口や湯道折りの清浄労力を低減し、鋳造品をパンチアウト後そのまま連続ショットに投入できることによって清浄作業場の環境改善や湯道などの再ショット工程の省略、戻しによる電気炉でのノロ発生の削減、また棚吊りなどによる炉の損傷の軽減など計り知れない効果をもたらしてきました。しかし、全製品に展開するには勢力的な改善が必要で工場経営側の理解と技術者や現場の担当者の汗と努力の結晶とその発想の豊かさときめ細かな工夫に先人達の情熱には頭が下がります。
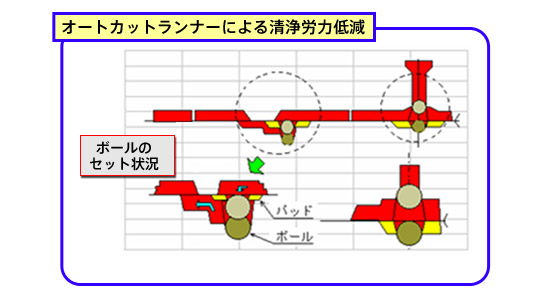
図2 オートカットランナーの原理(シェルボールが湯口を切断します)
また、生砂鋳型用の材料として植物油を採用して30年が経過しています。開発当時から石炭粉にかわる炭素質分として着目してきました、近年ではカーボンニュートラルな材料として環境に優しい鋳物作りに一役買っていることが再認識されています。
中子工法もいち早くウレタン系コールドボックス法を取り入れ、大物用にはウレタン系自硬性工法を採用しております。シェルと加えて主に3つの工法を製品毎に設定し品質の安定を図っています。
仕上げでは研削よりも旋削を主に処理工程としています。鋳造方案でバリレス、湯口部の折りっ放しを追及し、鋳仕上げレスを目指していますが、方案対策だけではカバー出来ない部分を除去するという考え方です。もちろん、エキマニなどは清浄ラインに近接してNCグラインダーなどを組み合わせて横持ちレスを推進しています。
また鋳造工場として、現在では珍しくなくなりましたが全員で行う3Sや定期的なPM(予防保全)活動も継続しています。
以上のように土浦素形材工場は環境改善と作業改善に積極的な取り組みを続けてきたということがお分かり戴けたでしょうか。